Waste Concrete Crushing Production Line: Efficient and Eco-Friendly Recycling for Construction Waste
Introduction: Turning Construction Waste into Valuable Resources
With the rapid pace of urbanization, building demolition generates a massive amount of construction waste, especially waste concrete. If left untreated, it leads to land occupation, environmental pollution, and resource waste. The waste concrete crushing production line offers a sustainable and efficient solution, transforming discarded concrete into high-quality recycled aggregates used in construction and infrastructure projects.
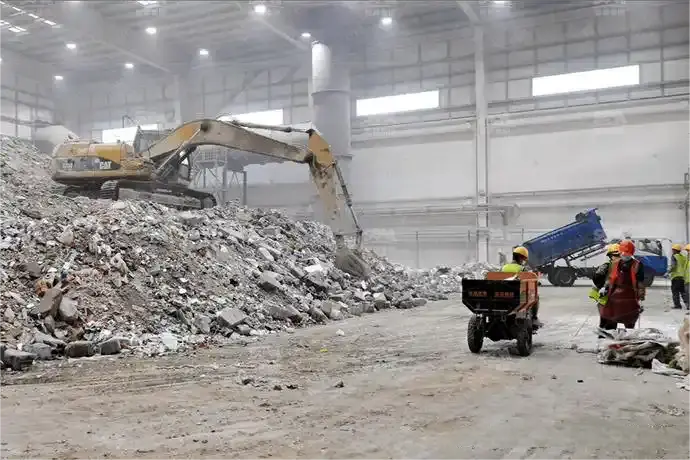
Crushing Process of the Waste Concrete Production Line
The overall process of the waste concrete crushing production line is streamlined and efficient, closely resembling a typical stone crushing line but optimized for reinforced concrete.
Step-by-step Process:
- Feeding and Pre-treatment: Waste concrete is transported to the site, where oversized blocks are broken down with hydraulic breakers. Long steel bars are manually removed or cut to prevent belt damage.
- Primary Crushing: The pre-treated concrete is fed into a jaw crusher, which crushes large chunks down to around 100mm.
- Secondary Crushing: The material then goes through an impact crusher (or cone crusher), further reducing it to 50mm or below.
- Rebar Separation: During crushing, embedded steel rebar is effectively separated and removed using a magnetic separator, ensuring cleaner end products.
- Screening and Final Products: A vibrating screen classifies the crushed materials into 0-5mm and 5-50mm fractions, ready for reuse in construction applications.
This intelligent process ensures consistent particle size, minimal impurities, and stable performance under continuous operation.
Equipment Configuration: High Efficiency and Low Energy Consumption
The equipment selection in a waste concrete crushing production line is crucial for maximizing productivity and minimizing maintenance. Typical equipment includes:
- Vibrating Feeder: Ensures even feeding and prevents blockages.
- Jaw Crusher: Handles hard concrete and initial size reduction.
- Impact Crusher or Cone Crusher: Provides fine crushing with excellent particle shape.
- Sand Washer: Cleans fine particles to improve material quality.
- Vibrating Screen: Classifies the finished product by size.
- Conveyors and Magnetic Separator: Facilitate material transport and remove embedded steel.
All machines are designed for compact installation, low wear rate, and easy maintenance—making the line suitable for various environments.
Eco-Friendly and Economical: Double Benefits for Businesses
Using a waste concrete crushing production line provides significant environmental and financial advantages:
- ✔ Environmental Benefits: Reduces landfill usage and pollution. Dust collectors and noise reduction systems ensure compliance with local emission standards (up to 99% dust removal rate).
- ✔ Cost Reduction: Eliminates the need for raw stone aggregates. Recycled concrete aggregates can be used in the production of eco-bricks, pavement blocks, insulation bricks, and more.
- ✔ Government Incentives: Many regions offer tax benefits, subsidies, or incentives for businesses adopting green construction practices and recycling technologies.
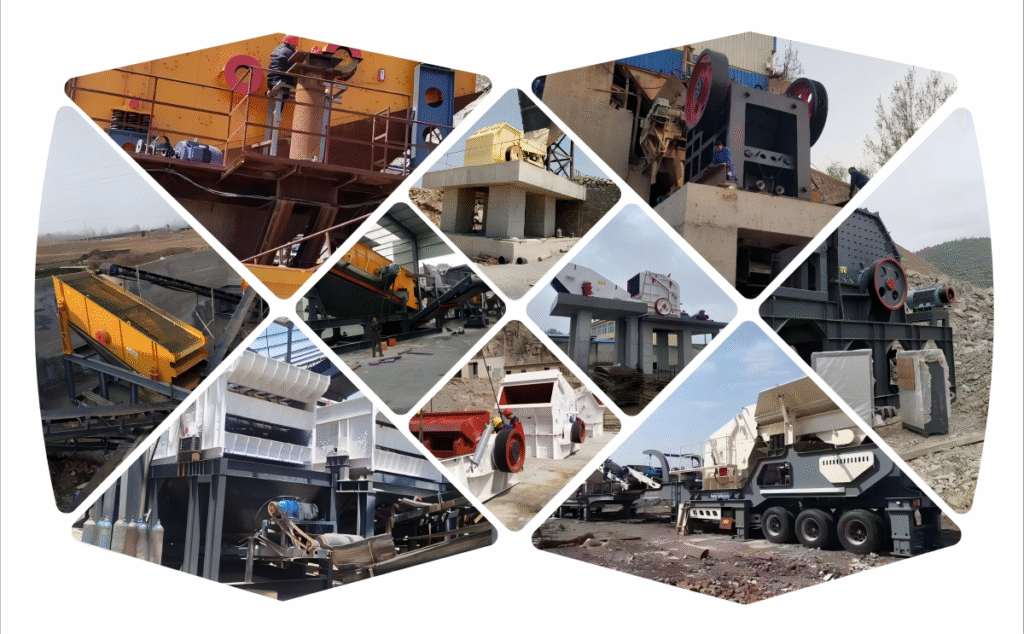
Stationary vs. Mobile Crushing Solutions
The production line is available in both stationary and mobile versions to meet different project needs:
- Stationary Crushing Line: Suitable for large-scale, centralized waste processing plants. High throughput and stable operation.
- Mobile Crushing Station: Offers on-site processing flexibility. Ideal for urban demolition sites, roadworks, and decentralized locations. Reduces transport costs and setup time.
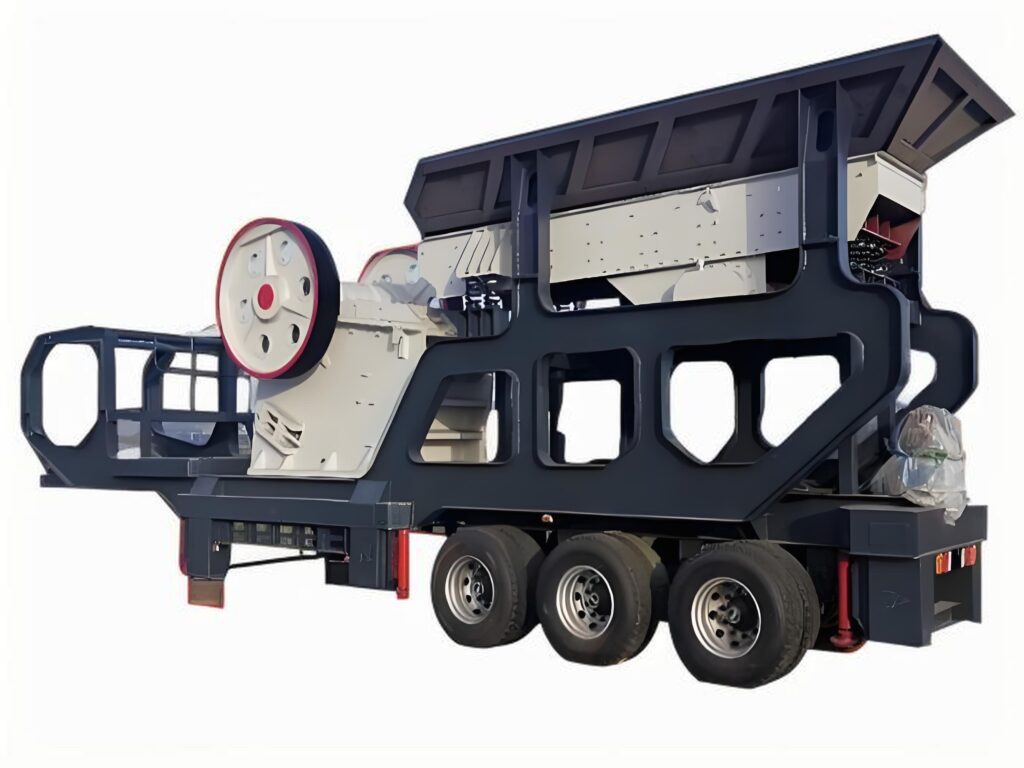
Application Scenarios and Market Potential
The waste concrete crushing production line is widely used in:
- Urban demolition and reconstruction
- Infrastructure upgrades
- Prefabricated concrete recycling
- Road base and backfill material production
With increasing environmental regulations and the push for sustainable construction, the demand for efficient recycling systems is expected to surge globally. This makes the crushing production line a profitable and future-proof investment.
Frequently Asked Questions (FAQ)
Q1: What is the capacity of a typical waste concrete crushing production line?
A: It ranges from 50 to 300 tons per hour depending on the configuration. Custom solutions are available.
Q2: Can steel rebar be fully removed from crushed concrete?
A: Yes. The system includes magnetic separators that effectively remove steel rebar, producing clean recycled aggregates.
Q3: Can the system operate at demolition sites?
A: Absolutely. The mobile version is specifically designed for on-site use with easy transport and fast setup.
Q4: What are the end uses of the recycled concrete aggregates?
A: They can be used in paving bricks, base layers, concrete blocks, and even as raw material for cement production.
Q5: How environmentally friendly is the production process?
A: The system is equipped with dust collection and noise control features, ensuring compliance with environmental standards.
Ready to Start Recycling Smarter?
Invest in a waste concrete crushing production line and turn construction waste into value. Contact our technical team for customized solutions, equipment quotations, and site layout recommendations.
Home – Premium Crushing Solutions for Global Mining & Construction
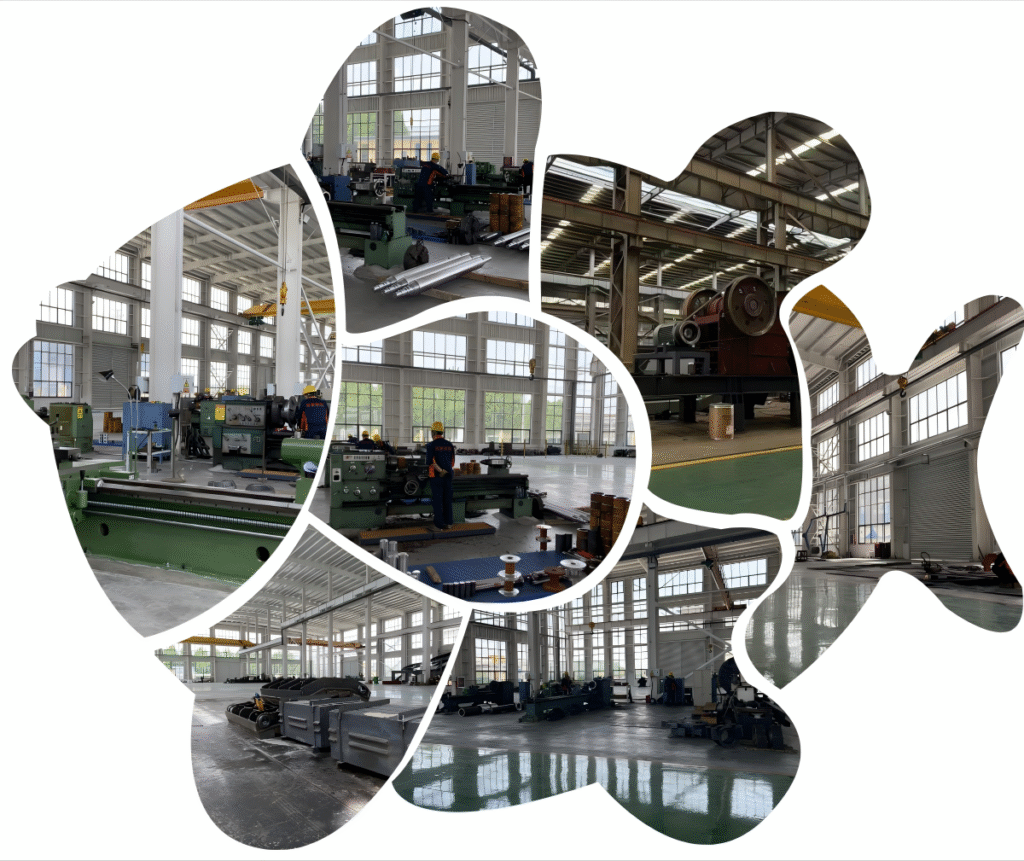