Feeding Methods and Precautions for Primary Crushers
Introduction
In the field of mining and aggregate production, primary crushers (also known as 粗破碎机) play a critical role as the first stage of material size reduction. Whether using jaw crushers, gyratory crushers, or primary cone crushers, the feeding method and operational precautions greatly influence production efficiency, equipment lifespan, and safety.
This article explores the most common feeding methods for primary crushers, essential precautions during operation, and best practices for optimal performance.
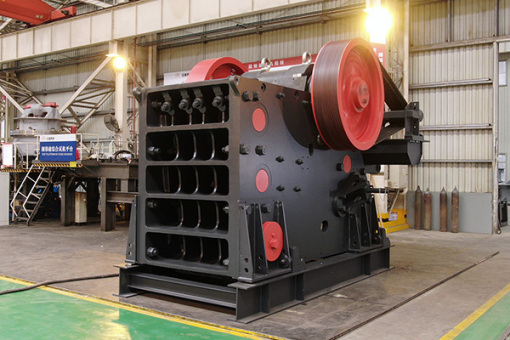
Feeding Methods for Primary Crushers
1. Feed Hopper Design
The size of the feed hopper is directly related to factors such as:
- The dumping method (e.g. truck tipping, loader feeding)
- Volume per dump
- Dumping interval time
For large-scale primary crushers, the effective volume of the hopper typically ranges from 100 до 200 tons. A well-sized hopper allows buffer storage, ensures consistent feed, and reduces the likelihood of crusher choking or idle time.
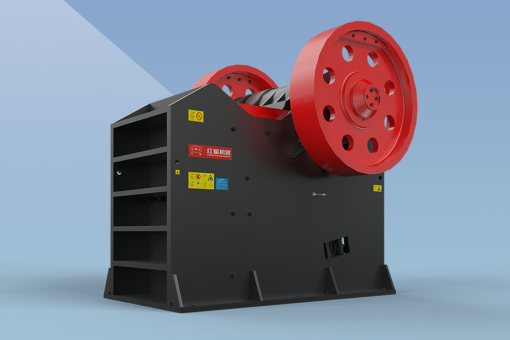
2. Feeder Types
Under the feed hopper, the choice of feeder should be based on the crusher size and material characteristics:
- Heavy-duty apron feeders are ideal for large jaw or gyratory crushers. These feeders can handle high-impact loads and large feed sizes.
- Medium-duty apron feeders або large electromagnetic vibrating feeders are more suitable for small and medium primary crushers.
Note:
The width of the feeder should be at least twice the maximum feed size of the material, ensuring smooth flow and preventing blockages.
3. Protective Design
To avoid damage during material dumping:
- The inner walls (especially rear and sides) of the feed hopper should be lined with steel rails or thick wear plates.
- Hopper shape must allow free material flow to prevent bridging and material hang-ups.
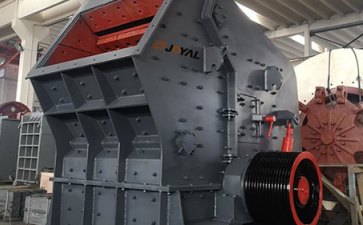
Operational Precautions for Primary Cone Crushers
Taking a coarse crushing cone crusher as an example, observe the following to ensure safe and efficient operation:
1. Pre-Start Checklist
- Inspect lubrication system thoroughly.
- Check cone chamber for blockages or residual material.
- Ensure belt tension is correct and bolts are fully tightened.
2. Startup Procedure
- Start the oil pump motor 5–10 minutes in advance.
- Confirm lubrication is functioning properly before starting the main motor.
3. Feeding During Operation
- Run the crusher under no load for 1–2 minutes before feeding.
- Feed should be choke-fed (full chamber feeding) to optimize crushing efficiency.
- With high moisture або clay-rich ores, monitor feed conditions closely to prevent clogging.
- Ensure no ore is accumulating under the sealing assembly, which can affect performance.
4. Shutdown Procedure
- First, stop feeding.
- Once all material is discharged, then shut down the main motor.
- Finally, stop the oil pump motor.
- After shutdown, conduct a full inspection and address any faults.

Best Practices for Feeding Control
To achieve higher automation and equipment protection, the apron feeder should ideally be equipped with variable frequency drive (VFD). This allows real-time adjustment of the feeding rate based on crusher load and downstream capacity.
Additionally:
- Always maintain a buffer layer of material in the hopper.
- Avoid dumping large rocks directly onto the feeder chains to prevent mechanical damage.
Часті запитання (Поширення)
Q1: Why is choke feeding recommended for cone-type primary crushers?
A: Choke feeding ensures the crushing cavity remains full, which improves crushing efficiency and reduces wear by providing a cushion for the rock-on-rock crushing action.
Q2: What happens if the feeder width is too small?
A: A narrow feeder may cause material hang-ups, lead to uneven feeding, or force oversized rocks through smaller openings—risking mechanical damage and decreased capacity.
Q3: Can vibrating feeders be used for all types of primary crushers?
A: Not always. Vibrating feeders are more suited for medium feed sizes. For large and heavy boulders, apron feeders are more robust and reliable.
Q4: How to prevent damage to the hopper during material dumping?
A: Reinforce hopper walls with steel plates or rails, and design the feed chute with appropriate impact-absorbing linings to distribute the force of falling rocks.
Зв’яжіться з нами
Need help selecting the right feeding solution for your primary crusher? Our engineering team is ready to support you with customized layouts and equipment.
👉 Contact Us Now
Let’s build smarter crushing systems together!