How to Choose the Right Crusher for Your Application
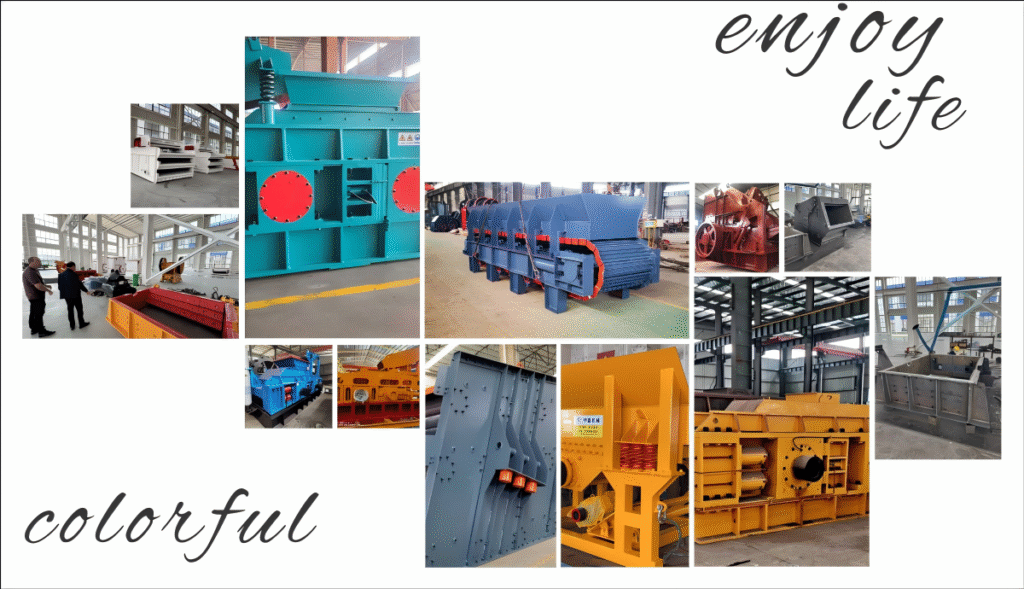
Selecting the right crusher is a critical decision that impacts your productivity, operational cost, and product quality. With so many crusher types on the market—jaw crushers, cone crushers, impact crushers, hammer crushers, and more—how do you know which one fits your needs?
This guide will walk you through the key considerations when choosing the ideal crusher for your application.
1. Understand Your Material
The first step is to evaluate the physical properties of the raw material:
Property | Impact on Crusher Choice |
---|---|
ความแข็ง | Harder materials require more robust crushers like jaw or cone crushers. |
Abrasiveness | Highly abrasive materials wear down hammers or blow bars faster. Choose wear-resistant materials. |
Moisture content | Wet materials can clog crushers with tight discharge gaps, such as fine jaw crushers or impact crushers. |
Size and shape | Large boulders require primary crushers (e.g., jaw crushers) to reduce feed size. |
2. Define Your Final Product Requirements
What’s the desired output?
- Crushing ratio: Do you need coarse, medium, or fine crushing?
- Particle shape: For high-quality aggregates or sand, use impact crushers or vertical shaft impact (VSI) crushers.
- Capacity: Match the crusher’s throughput to your production goals.
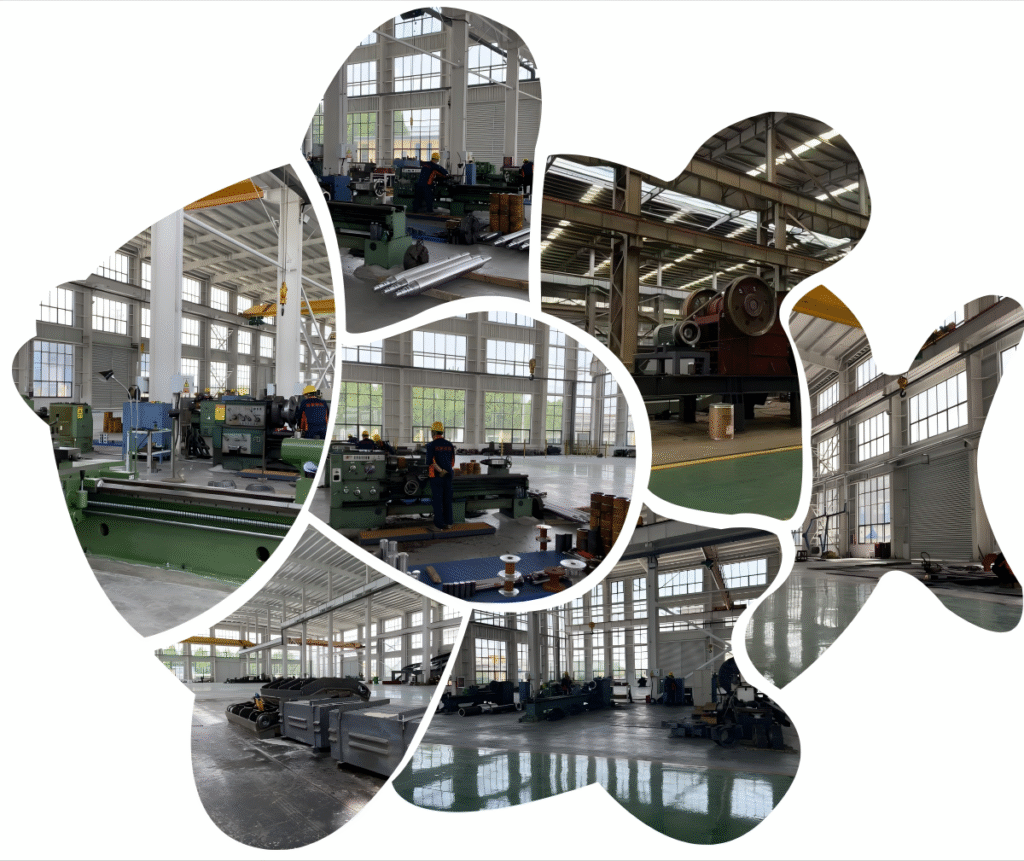
3. Common Crusher Types and Their Applications
🔷 Jaw Crusher
Best for: Primary crushing of hard, abrasive materials (e.g., granite, basalt).
Output: Coarse fragments.
ข้อดี:
- Simple structure, easy maintenance.
- High crushing ratio.
🔷 Cone Crusher
Best for: Secondary or tertiary crushing of hard, abrasive rocks.
Output: Well-shaped aggregates, medium to fine size.
ข้อดี:
- High efficiency.
- Consistent particle size.
🔷 Impact Crusher
Best for: Medium-hard materials like limestone, concrete, coal.
Output: Cubical particles, used in construction aggregates.
ข้อดี:
- High reduction ratio.
- Good shaping ability.
🔷 Hammer Crusher
Best for: Soft to medium-hard materials (e.g., gypsum, หินปูน, bricks).
Output: Fine crushing.
ข้อดี:
- Simple design.
- High crushing speed.
🔷 VSI (Vertical Shaft Impact) Crusher
Best for: Sand making, shaping fine aggregates.
Output: Uniform, cubical sand.
ข้อดี:
- Excellent for producing high-quality manufactured sand.
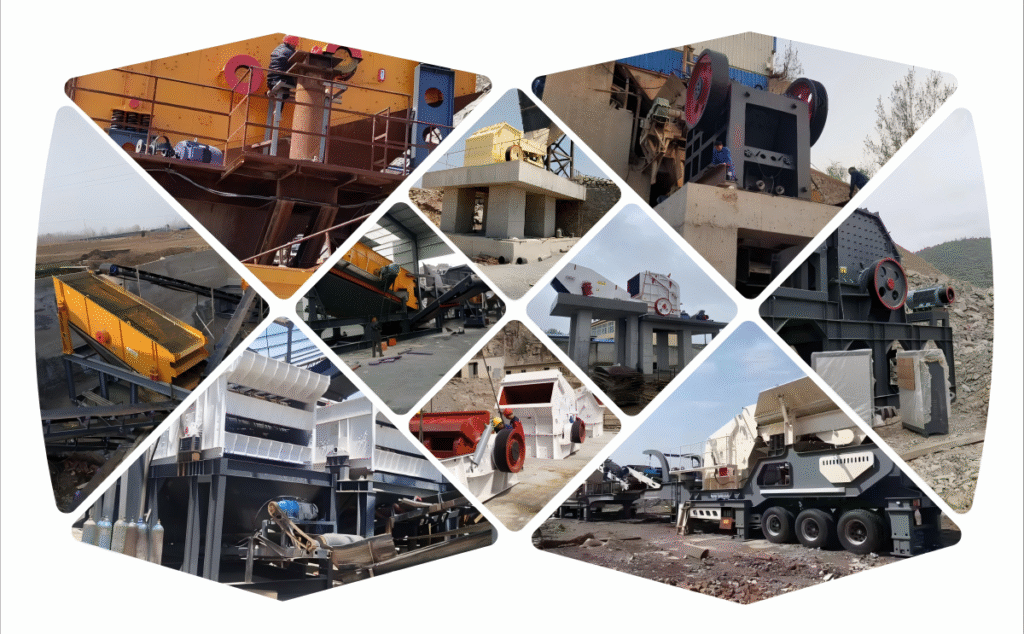
4. Consider Operational Factors
Before choosing a crusher, consider:
- Mobility: กับเครื่องเขียน. เครื่องบดเคลื่อนที่. Mobile crushers are ideal for on-site flexibility.
- Automation and control systems: Modern crushers come with sensors and software to optimize performance.
- Maintenance: Look for ease of access and availability of spare parts.
- Energy consumption: Energy-efficient machines reduce operational costs.
5. Budget vs. Long-Term Value
The cheapest machine may cost more in the long run. Consider:
- Wear part costs
- Downtime risk
- Replacement frequency
- Energy use
Summary: Crusher Selection Cheat Sheet
Application | Recommended Crusher |
---|---|
Hard, coarse materials (primary) | เคอร์เซอร์กราม |
Medium-hard materials (secondary) | เครื่องบดกรวย |
Fragile, medium-hard (shaping) | Impact Crusher |
Soft, brittle materials | Hammer Crusher |
Sand production | VSI Crusher |
Need Help Choosing the Right Crusher?
Still unsure which crusher fits your application? Let our experts help you choose a machine that maximizes your ROI.
👉 Contact Us Today for a free consultation and tailored solution.
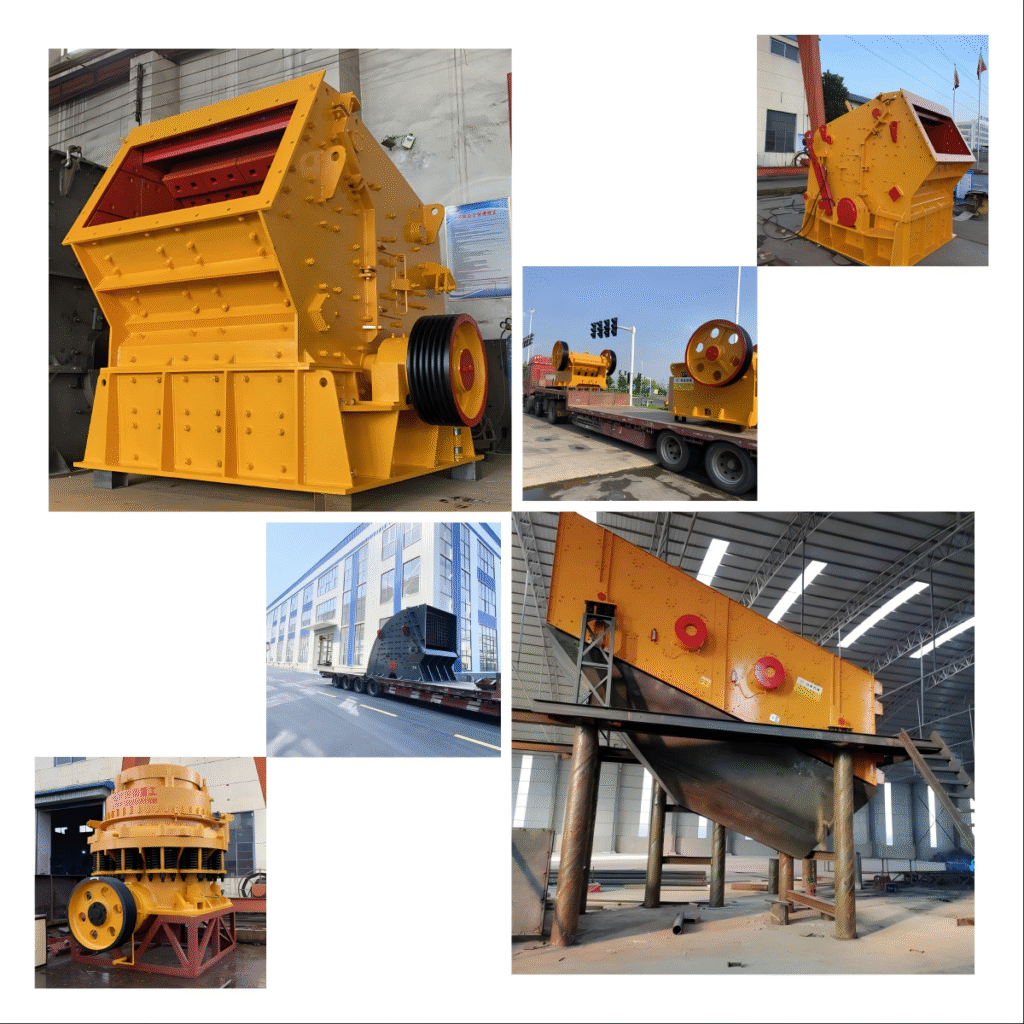