How to Choose Crushing Equipment for Quarries and Non-Ferrous Metal Mines? — A Guide to Three Core Machines
In the fields of quarrying and non-ferrous metal mining, crushing is a critical stage in the entire production process. Selecting the right crushing equipment not only improves productivity and efficiency but also reduces operating costs. This article provides a comprehensive comparison of JE Jaw Crusher, Impact Crusher, and Hammer Crusher, covering material suitability, working principles, and application scenarios — helping you make informed equipment choices for your stone and mineral processing needs.
1. Crushing Demands in Quarries and Non-Ferrous Metal Mines
Quarries mainly deal with hard rock materials such as granite, basalt, and limestone, while non-ferrous metal ores (like copper, lead-zinc, nickel, etc.) often feature complex mineral compositions that require highly durable equipment with consistent output control.
Key considerations for equipment selection include:
- Material hardness and moisture
- Input and output size requirements
- Crushing ratio and processing capacity
- Maintenance cost and wear part replacement cycles
2. JE Jaw Crusher: The Ideal Choice for Primary Crushing
The JE Series Jaw Crusher is designed for primary crushing of large-sized rocks and ores. With its robust frame and deep crushing chamber, it is widely used in quarrying and mining operations.
Key Advantages:
- High crushing ratio: Effective for various hard rocks and ores
- Durable structure: High-manganese steel casting, wear-resistant
- Easy maintenance: Hydraulic adjustment system reduces downtime
- Energy-efficient: Optimized motor design saves power
Application Scenarios:
Perfect for primary crushing of limestone, iron ore, copper ore, and similar materials — the first step in your stone crushing plant.
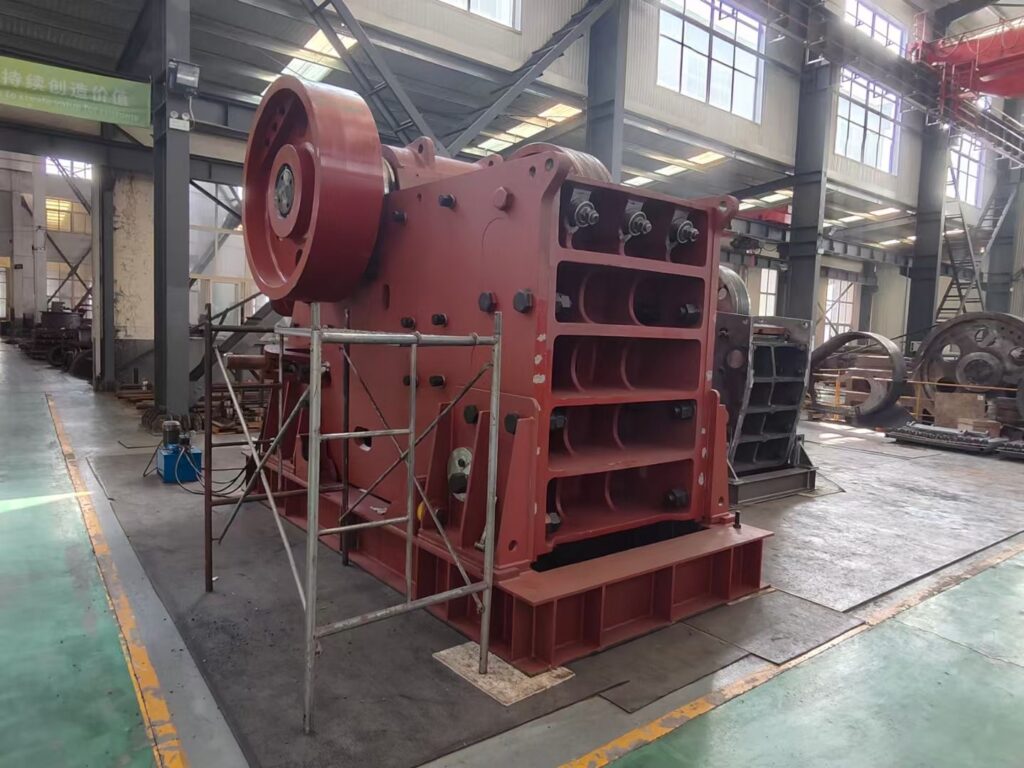
3. Impact Crusher: The Go-To for Secondary Crushing and Shaping
The Impact Crusher is used for medium-hard materials and serves as a secondary crusher. It also offers superior shaping ability, ideal for aggregate production with strict particle shape requirements.
Key Advantages:
- Excellent final product shape: Cubic output with low needle content
- Flexible adjustment: Discharge size can be controlled via impact plate
- Compact design: Easy to install and integrate into crushing lines
- Versatile usage: Ideal for construction aggregates and road materials
Application Scenarios:
Best suited for crushing medium-hard stones like dolomite and limestone, as well as some silicon-bearing metal ores.

4. Hammer Crusher: A Versatile and Efficient Option
The Hammer Crusher is designed for medium and low hardness materials and is capable of both medium and fine crushing. In some setups, it can even replace a two-stage system.
Key Advantages:
- One-time forming: Reduces need for secondary crushers
- High-efficiency rotor: Delivers better throughput
- Easy to service: Quick hammer head replacement, reliable operation
- Moisture tolerance: Some models support slightly wet materials
Application Scenarios:
Suitable for crushing coal gangue, gypsum, shale, bauxite, and other mineral materials.
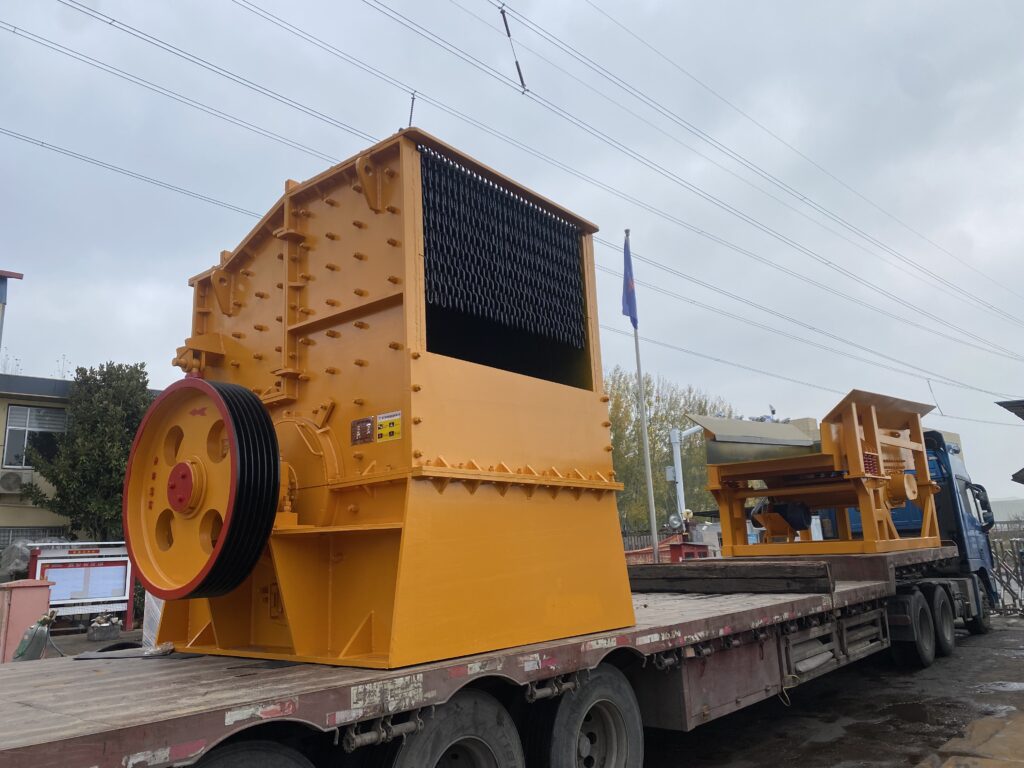
5. Conclusion: Smart Equipment Choices Boost Mining Efficiency
Selecting the right crushing equipment is vital for improving efficiency and reducing energy consumption. For quarry and non-ferrous metal mine operators, the combination of JE Jaw Crusher, Impact Crusher, and Hammer Crusher offers flexibility to meet various processing needs — from primary to fine crushing.
Looking for high-performance and durable mining crushers?
👉Дом – Премиальные решения для сокрушительных решений для глобальной добычи & Строительство for tailored solutions and competitive pricing!
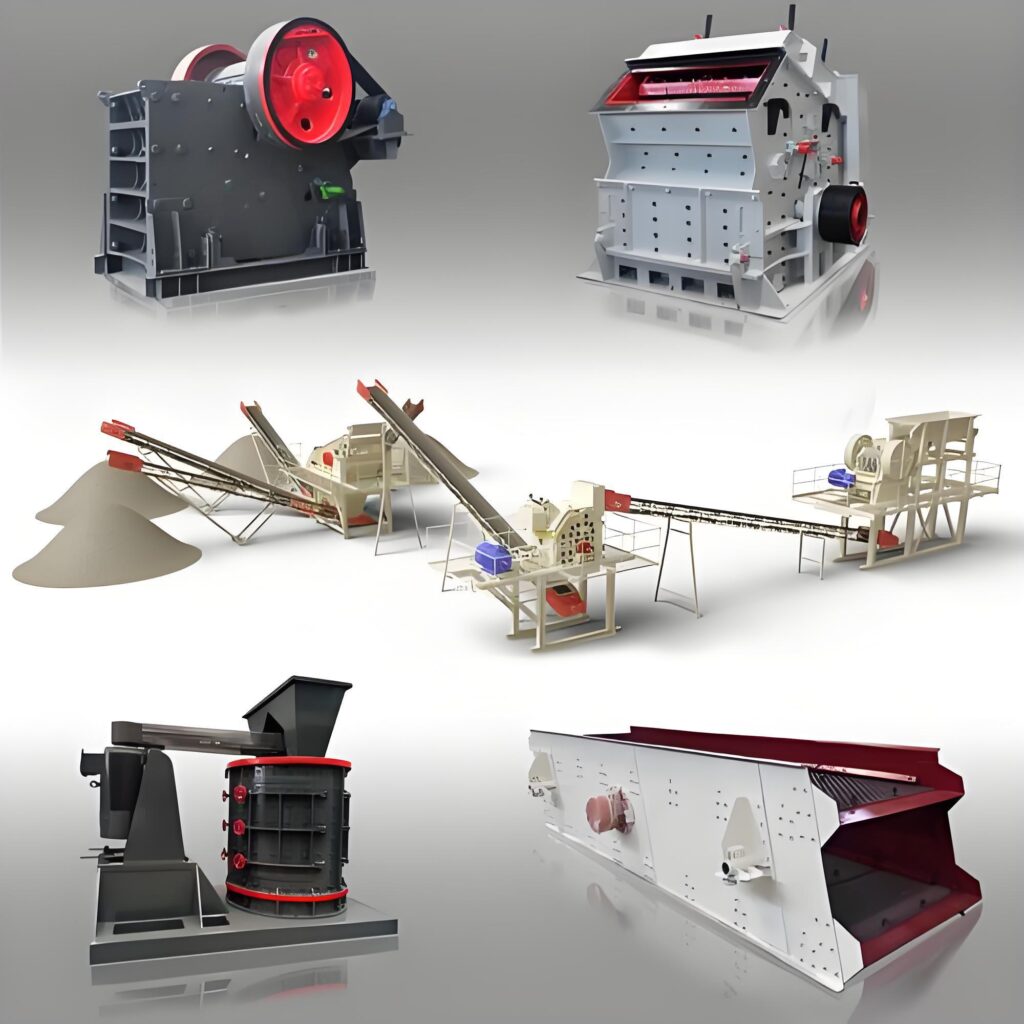