8 Common Causes of Impact Crusher Blockage and How to Solve Them
Impact crushers are widely used in mining, construction, cement, and other industries due to their high crushing efficiency, good particle shape, and reliable performance. However, during long-term operation, various factors such as raw material properties, component wear, and improper operation can lead to a common issue—blockage.
Blockage in an impact crusher not only affects production efficiency but may also damage the equipment and cause unplanned downtime. In this article, we’ll discuss 8 common causes of impact crusher blockage and provide effective solutions to help operators troubleshoot problems and maintain smooth production.
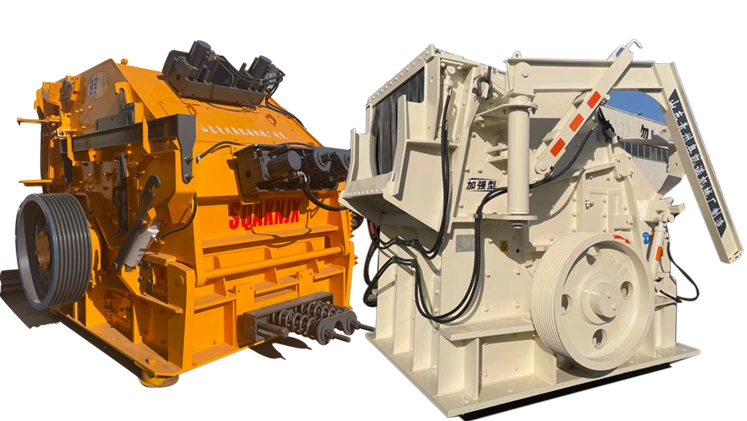
1. High Moisture Content Causes Material Adhesion
Symptoms:
Material sticks inside the crushing chamber or on the grate, reducing throughput.
Cause:
When the raw material contains too much moisture, it tends to adhere to the liner and grate, reducing the chamber volume and discharge efficiency.
Solutions:
- Preheat the impact plate and feed inlet
- Install drying equipment
- Sun-dry or air-dry raw materials to reduce moisture content
2. Material Too Hard, Too Much, or Oversized
Symptoms:
Crusher struggles to process material; discharge is blocked.
Cause:
If the material is too hard or large, or if too much is fed at once, it may not be fully crushed between the plate hammer and impact plate, leading to blockages.
Solutions:
- Ensure material meets the crusher’s specifications
- Limit the feed volume; install alarms or indicators to prevent overfeeding
- Pre-break oversized rocks before feeding
3. Feed Rate Too Fast or Discharge Too Slow
Symptoms:
Material accumulates inside the crusher; equipment overloads.
Cause:
When feeding exceeds discharge capacity, materials back up in the chamber, causing blockage and potential mechanical stress.
Solutions:
- Regulate feed speed based on processing capacity
- Adjust discharge port size as needed, especially when material characteristics change
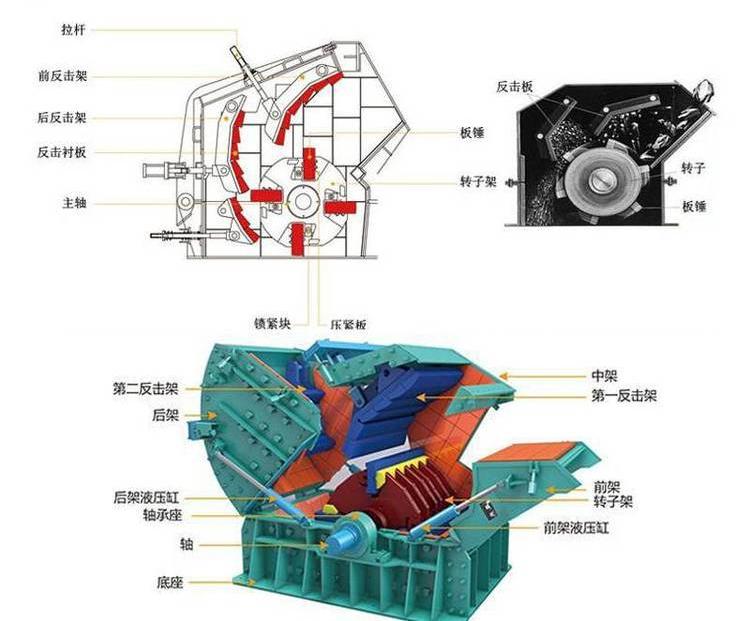
4. Loose V-Belt Reduces Transmission Power
Symptoms:
Material is only partially crushed or not discharged properly.
Cause:
If the V-belt is too loose, power cannot be effectively transferred to the rotor, affecting crushing and discharge performance.
Solutions:
- Regularly inspect and adjust belt tension
- Replace worn or damaged belts in time
5. Excessive Wear of Key Components
Symptoms:
Poor crushing performance; material builds up in the chamber.
Cause:
Worn impact plates or hammers reduce the crusher’s efficiency, making it harder for material to pass through smoothly.
Solutions:
- Inspect wear parts regularly
- Replace worn components to maintain optimal crushing performance
6. Damaged Main Shaft
Symptoms:
Machine halts unexpectedly; components fail to operate properly.
Cause:
The main shaft is critical to driving the crusher. Damage can disrupt the entire mechanism and result in blockage.
Solutions:
- Ensure proper lubrication and maintenance
- Repair or replace the main shaft promptly if issues are detected
7. Operator Error
Symptoms:
Frequent blockages; irregular machine behavior.
Cause:
Improper startup procedures, unfamiliarity with the equipment, or feeding errors can all lead to blockages.
Solutions:
- Provide formal training to operators
- Follow standard operating procedures for startup and feeding
- Inspect critical components like belts before use
8. Poor Crushing Chamber Design
Symptoms:
Frequent blockages in the lower part of the chamber.
Cause:
An ill-designed crushing chamber can cause material to accumulate in dead zones, especially at the discharge area.
Solutions:
- Use a curved crushing chamber design with a gradually decreasing nip angle to promote material flow
- Choose crushers from reputable manufacturers with proven design quality
- Retrofit or upgrade older machines if necessary

Home – Premium Crushing Solutions for Global Mining & Construction
To reduce the risk of impact crusher blockage, consider the following best practices:
✅ Control material size, hardness, and moisture content
✅ Monitor feed rate and adjust discharge accordingly
✅ Perform regular maintenance on wear parts and belts
✅ Train operators to follow standard procedures
✅ Select machines with optimized crushing chamber design
Need Support? Contact Our Expert Team
We provide professional support in impact crusher selection, custom solutions, spare parts supply, and technical services to help you avoid downtime and keep your operations running efficiently.
👉 Contact Us Now for expert guidance and fast assistance.
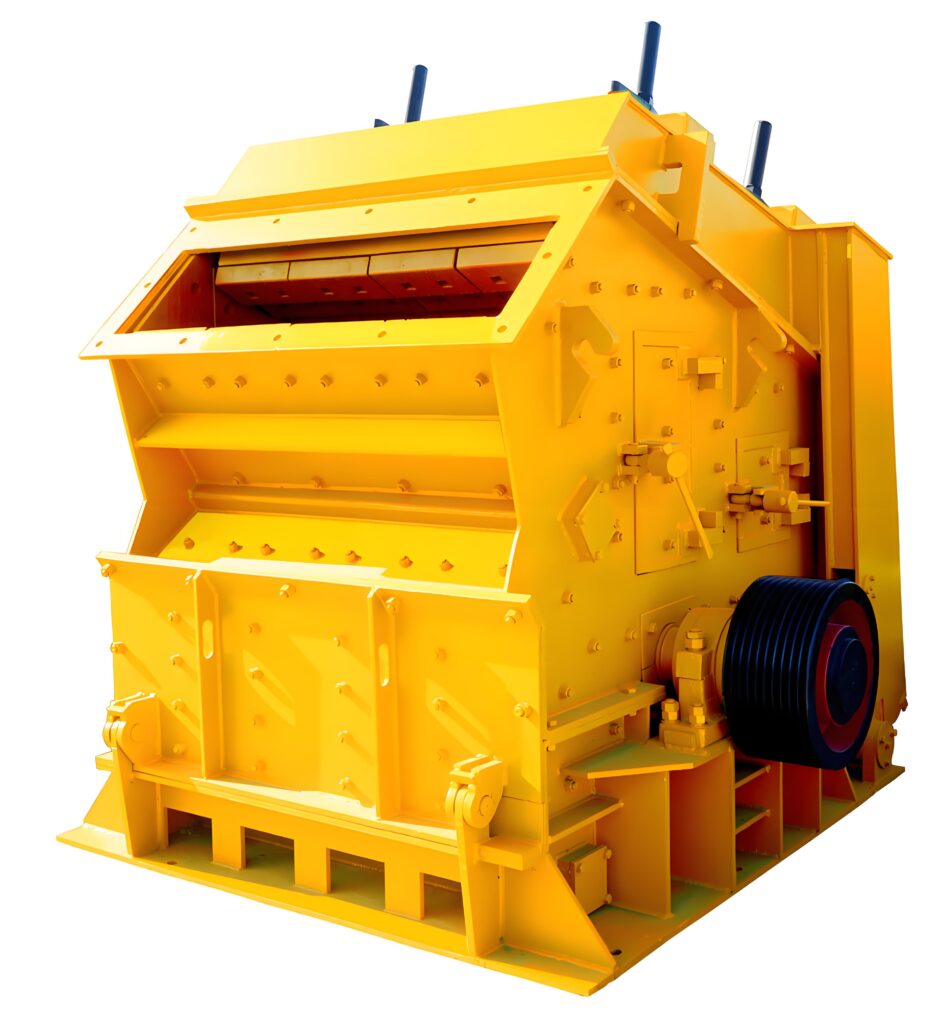