Ballast Crushing Process: Equipment, Workflow & Best Practices
What is Ballast and Why is it Important?
Ballast is the crushed stone or gravel laid underneath and around railway tracks to provide stability, drainage, and load-bearing support. It plays a crucial role in distributing the load from train traffic, preventing vegetation growth, and enabling proper water drainage. High-quality ballast ensures the safety, durability, and reliability of railway infrastructure.
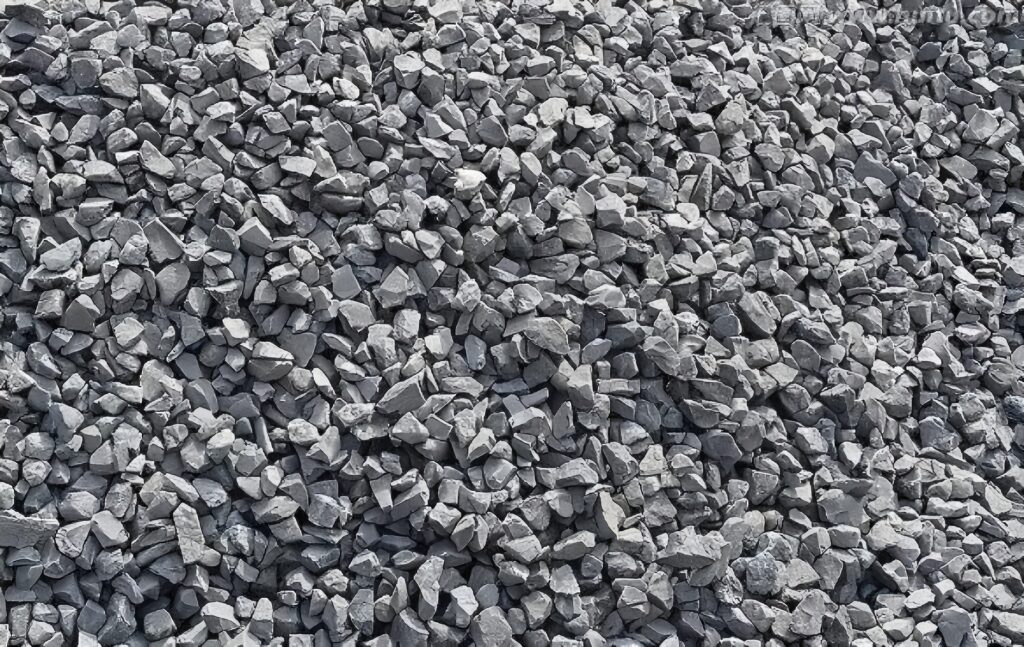
Overview of the Ballast Crushing Process
Producing railway ballast involves several stages of material preparation and crushing. The raw materials typically include hard rock types such as granite, basalt, limestone, or trap rock due to their high compressive strength and durability.
1. Raw Material Feeding
The process begins with the feeding of raw stones into the crushing system using vibrating feeders or dump trucks. The feeding equipment ensures a continuous and controlled flow of material into the primary crusher.
2. Primary Crushing
A jaw crusher is commonly used as the primary crushing unit. It breaks down large stones (typically >500mm) into smaller pieces (100–300mm), preparing them for secondary crushing. The key here is high reduction ratio and consistent feed size.
3. Secondary Crushing
In this stage, cone crushers or impact crushers are used to further reduce the stone size to the desired range. For ballast, the typical size ranges from 20mm to 63mm, depending on the rail standards and specifications.
4. Screening and Classification
After crushing, materials are passed through vibrating screens to classify them into different size fractions. Oversized particles are returned to the crushing circuit for further reduction. The final product must meet specific size and shape standards required by railway authorities.
5. Washing (Optional)
If the raw material contains clay or other impurities, a sand washing machine may be used to clean the crushed ballast, ensuring better performance in track beds.
6. Final Storage and Transport
Qualified ballast is then stockpiled or loaded for transport to railway construction sites. Belt conveyors or mobile loading stations are commonly used at this stage.
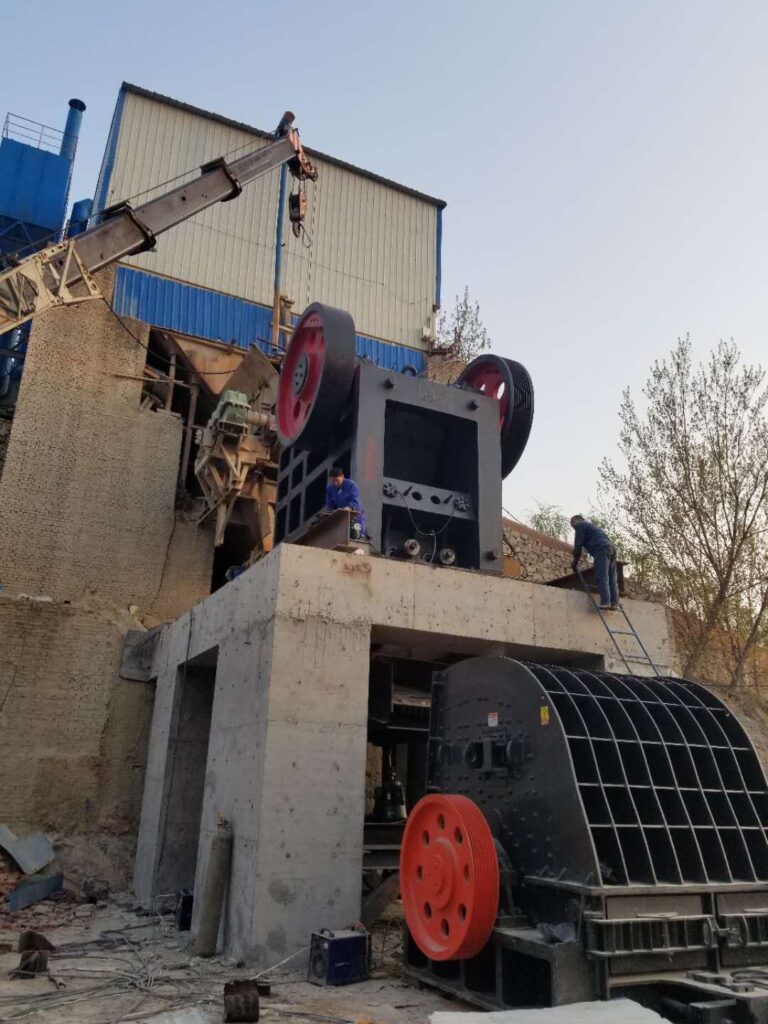
Recommended Equipment for Ballast Crushing Line
Equipment Type | Model Examples | Function |
---|---|---|
Jaw Crusher | PE600×900, PE750×1060 | Primary crushing |
Cone Crusher | HPC220, HPT300 | Secondary crushing |
Impact Crusher | PF1214, PF1315 | Shaping and refining |
Vibrating Screen | 3YK1548, 4YK2160 | Screening and sizing |
Vibrating Feeder | ZSW380×95, ZW1142 | Feeding materials |
Sand Washer (optional) | XSD2610, LSX920 | Cleaning impurities |
Belt Conveyor | B800, B1000 | Material transport |
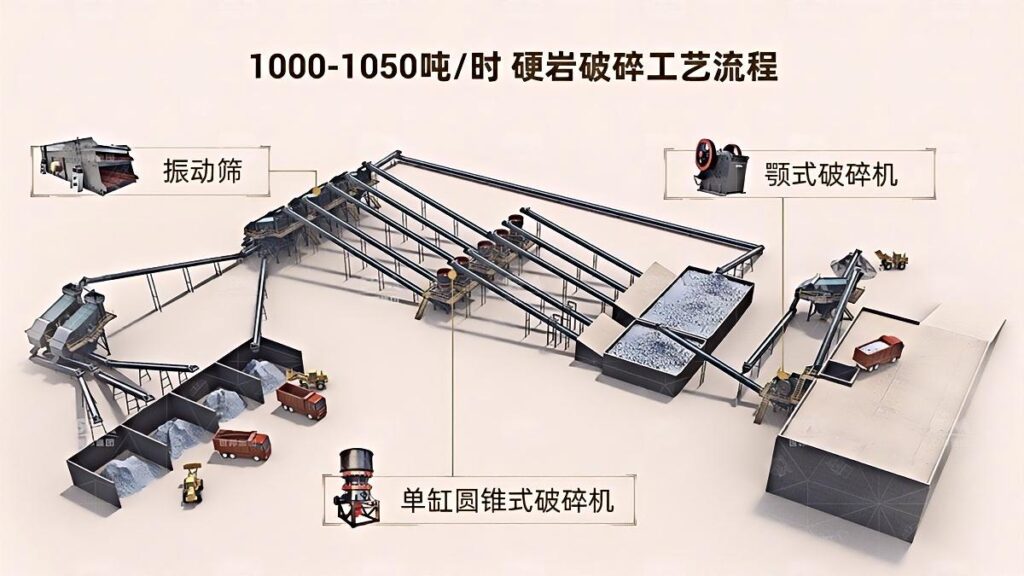
Benefits of an Optimized Ballast Crushing Process
- ✅ High productivity: Continuous crushing and screening reduce downtime.
- ✅ Consistent product quality: Well-graded and angular ballast for optimal rail support.
- ✅ Cost-effective: Reuse of oversize materials in a closed-loop system.
- ✅ Scalable: Can be adjusted to meet small or large-scale railway project demands.
Frequently Asked Questions (FAQ)
1. What is the ideal size of railway ballast?
The standard size of railway ballast typically ranges between 20mm and 63mm, depending on the country’s railway engineering standards. Proper gradation ensures optimal track performance and drainage.
2. What type of rock is best for ballast?
Hard and durable rocks like granite, basalt, and trap rock are ideal due to their high strength, resistance to weathering, and angular shape which improves interlocking.
3. Is sand or soft rock suitable for ballast?
No. Soft rock like limestone (unless hard grade) or sand degrades easily under pressure and is unsuitable due to poor load-bearing capacity.
4. Can recycled aggregates be used for ballast?
In some cases, recycled concrete or crushed rock can be used for sub-ballast or temporary tracks, but virgin hard stone is preferred for main railway lines to ensure durability and performance.
5. How much ballast is required per kilometer of track?
Typically, 2,000 to 2,500 tons of ballast is required per kilometer of single-track railway, depending on track design and terrain.
Conclusion
An efficient and well-planned ballast crushing process ensures the production of high-quality materials essential for the safe operation of railway lines. By using the right equipment and adhering to industry standards, manufacturers and contractors can deliver superior results while reducing operational costs.
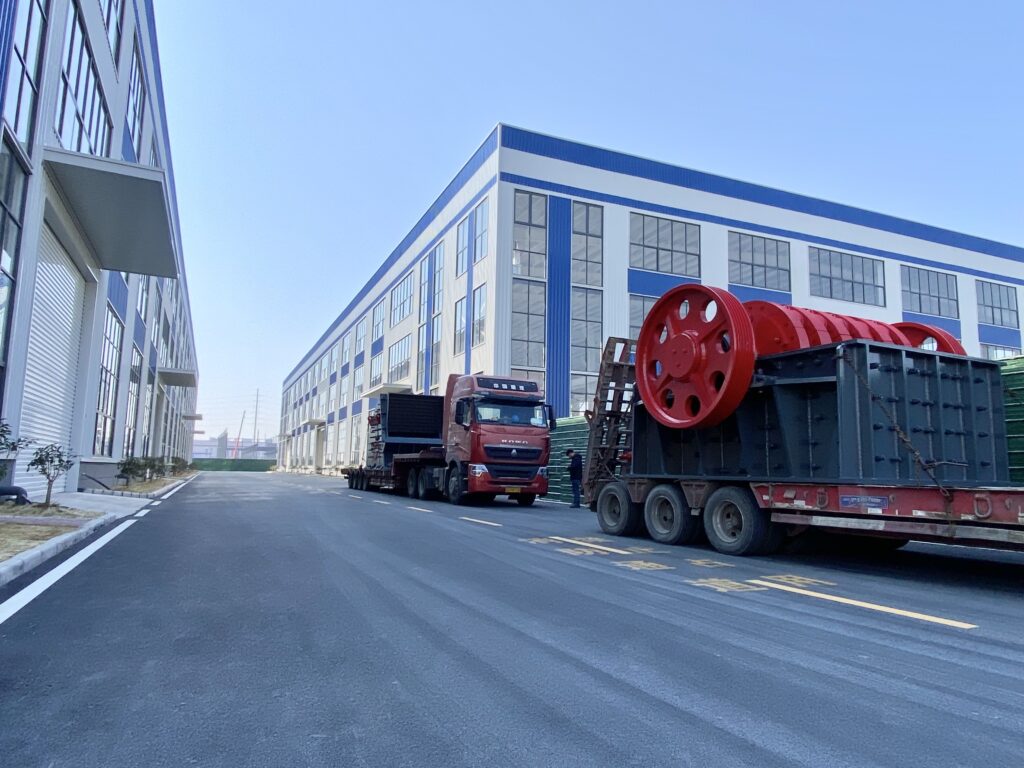