Crushing Methods for Concrete Aggregates: Common Sizes and Crusher Types
Concrete aggregate, also known as crushed stone for concrete, is one of the most essential components in the production of high-quality concrete. Selecting the proper crushing methods for concrete aggregates and the right type of crusher is crucial for ensuring consistent material size, strength, and workability.
In this article, we explore the three common size classifications of concrete aggregates and discuss three widely used types of concrete crushers, helping you determine the most suitable equipment for your operation.
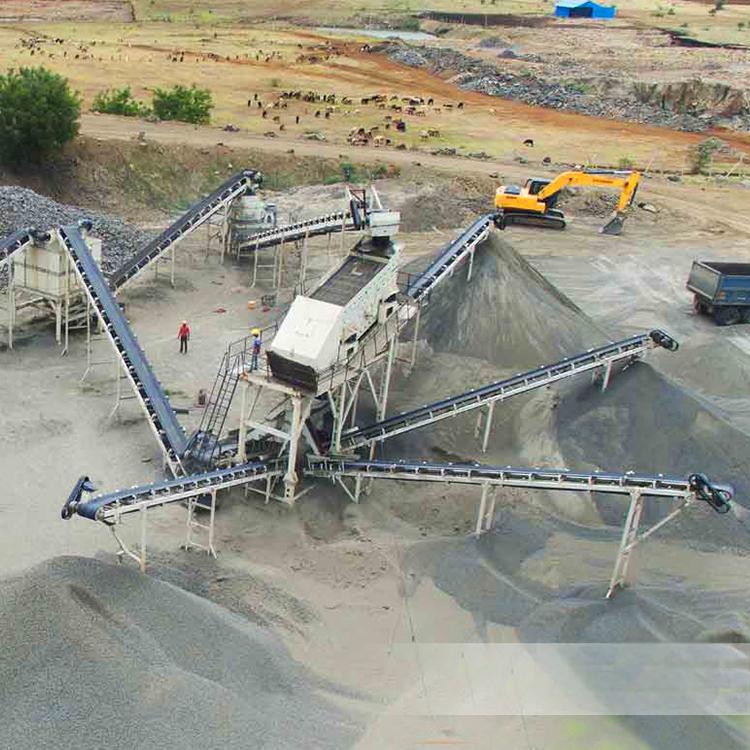
Common Aggregate Sizes for Concrete Production
Concrete aggregate is typically divided into three main size categories based on its particle diameter. Each category plays a specific role in the performance and structure of the final concrete mix.
1. Coarse Aggregate (10–30mm)
- Function: Provides the bulk density and compressive strength of the concrete.
- Use Case: Common in structural concrete such as columns, beams, and foundations.
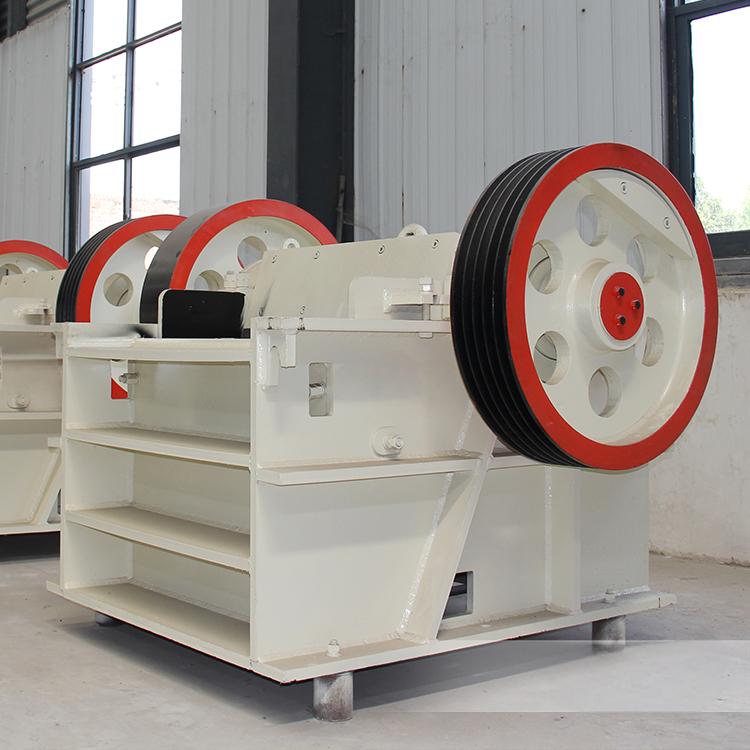
2. Medium Aggregate (5–10mm)
- Function: Enhances workability and reduces the amount of cement required.
- Use Case: Often used in general-purpose concrete for slabs and paving.
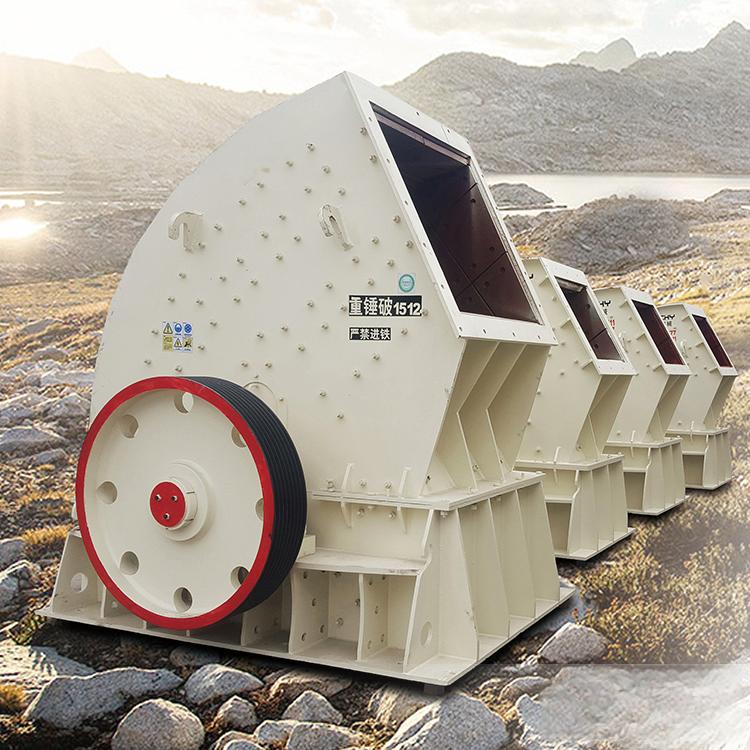
3. Fine Aggregate (1–5mm)
- Function: Improves impermeability and reduces the risk of cracking.
- Use Case: Ideal for finishing concrete surfaces, mortar, and precast products.
⚠️ Choosing the appropriate aggregate size is crucial for optimizing performance, reducing cement usage, and preventing structural issues in concrete.
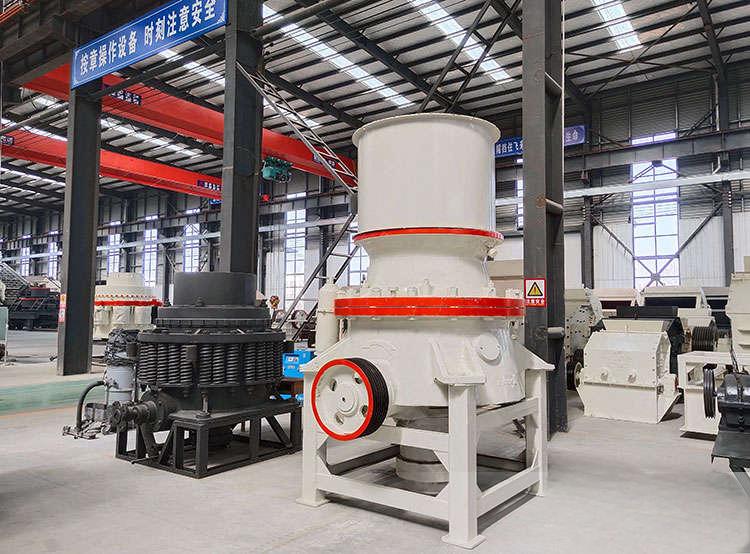
Types of Concrete Crushers and Their Advantages
Selecting the right crusher depends on your production capacity, material hardness, moisture levels, and particle size requirements. Below are three popular crusher types used for processing concrete aggregates:
1. Jaw Crusher – Best for Primary Crushing
A jaw crusher is ideal for initial crushing of large concrete blocks and construction waste.
Advantages:
- ✅ Deep crushing chamber with no dead zone, allowing large feeding volumes and efficient output.
- ✅ Made with wear-resistant materials for high durability and fewer breakdowns.
- ✅ Low noise output for a more environmentally friendly operation.
2. Swaar hamerbreker – Ideal for One-Time Shaping
The heavy hammer crusher is suitable for processing medium-hard to soft concrete material in a single stage.
Advantages:
- ✅ Fully sealed design prevents dust leakage and maintains a clean working environment.
- ✅ High-impact hammer head improves crushing efficiency and extends service life.
- ✅ Produces uniform, well-shaped aggregates that meet high-quality concrete standards.
3. Cone Crusher – Ideal for Secondary and Fine Crushing
Cone crushers are excellent for producing high-quality fine and medium aggregates with precision.
Advantages:
- ✅ Layered crushing principle increases cube content and improves aggregate shape.
- ✅ Reliable structure and optimized technology reduce downtime and maintenance costs.
- ✅ Easy disassembly for quick inspection and repairs, saving time and labor.
How to Choose the Right Crusher for Concrete Aggregates?
Choosing the right equipment depends on several factors:
- Material Type & Hardness: Granite, limestone, recycled concrete, etc.
- Daily Output Requirements: Measured in tons per hour.
- Mobility Needs: Stationary vs. mobile crushers.
- Budget: Includes both initial cost and maintenance expenses.
📌 Pro Tip: For mobile and flexible operations, many users prefer mobile crushing and screening units that combine multiple functions in one compact system.
FAQ: Concrete Aggregate Crushing
Q1: What’s the best method to crush concrete for high-strength concrete?
A: Use a jaw crusher for primary crushing and a cone crusher or heavy hammer crusher for secondary crushing to ensure proper particle gradation.
Q2: Can crushed recycled concrete be used as aggregate?
A: Yes, with proper processing and grading, recycled concrete can replace natural aggregates in many applications.
Q3: How to reduce dust during concrete crushing?
A: Choose sealed equipment like heavy hammer crushers and add dust suppression systems such as water sprays or bag filters.
Q4: What is the typical output size after crushing?
A: Most crushers can be adjusted to produce 1–30mm particle sizes depending on the desired aggregate specification.
Contact Us for Custom Crushing Solutions
At SL Mining Machinery, we offer customized concrete crushing equipment tailored to your project needs, material characteristics, and production goals.
📞 Contact our expert team today for a free consultation and quote!
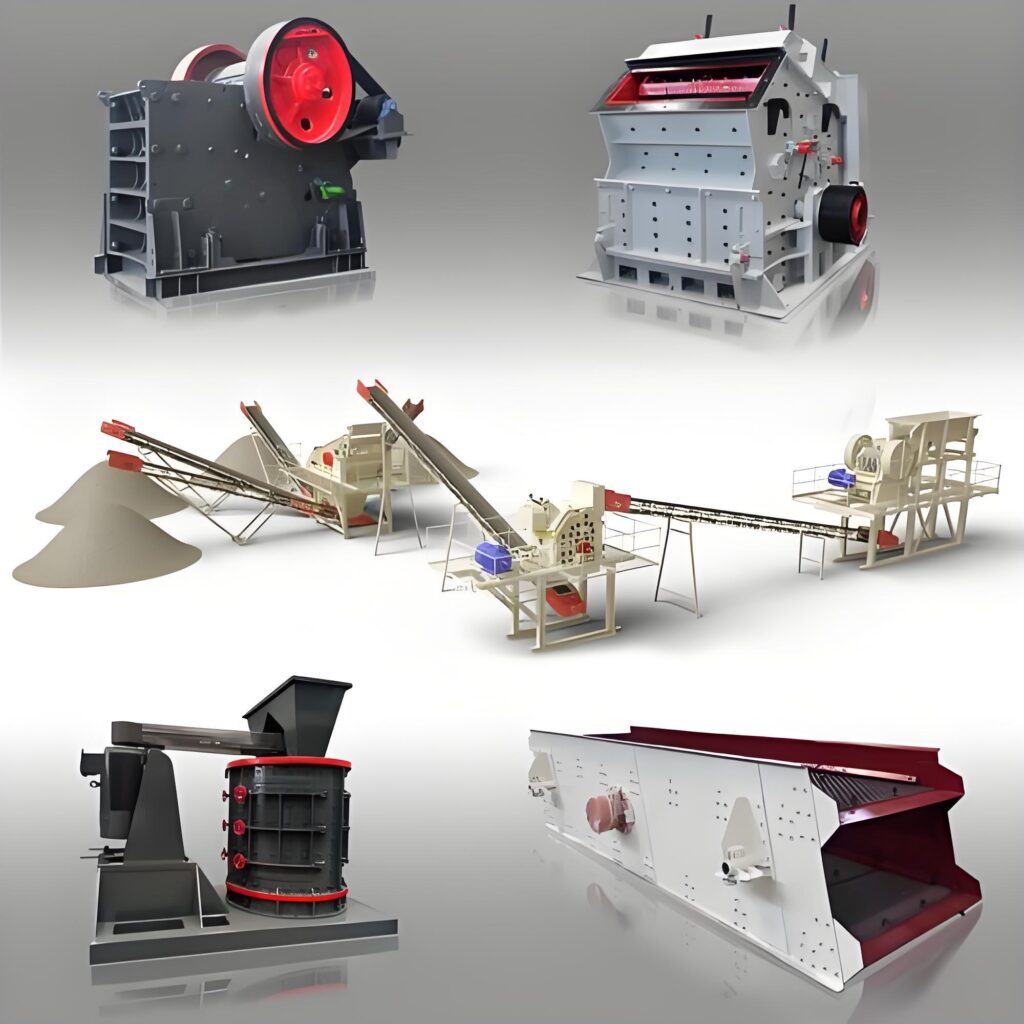